Interview with Prof. Dr. Friedrich Franek
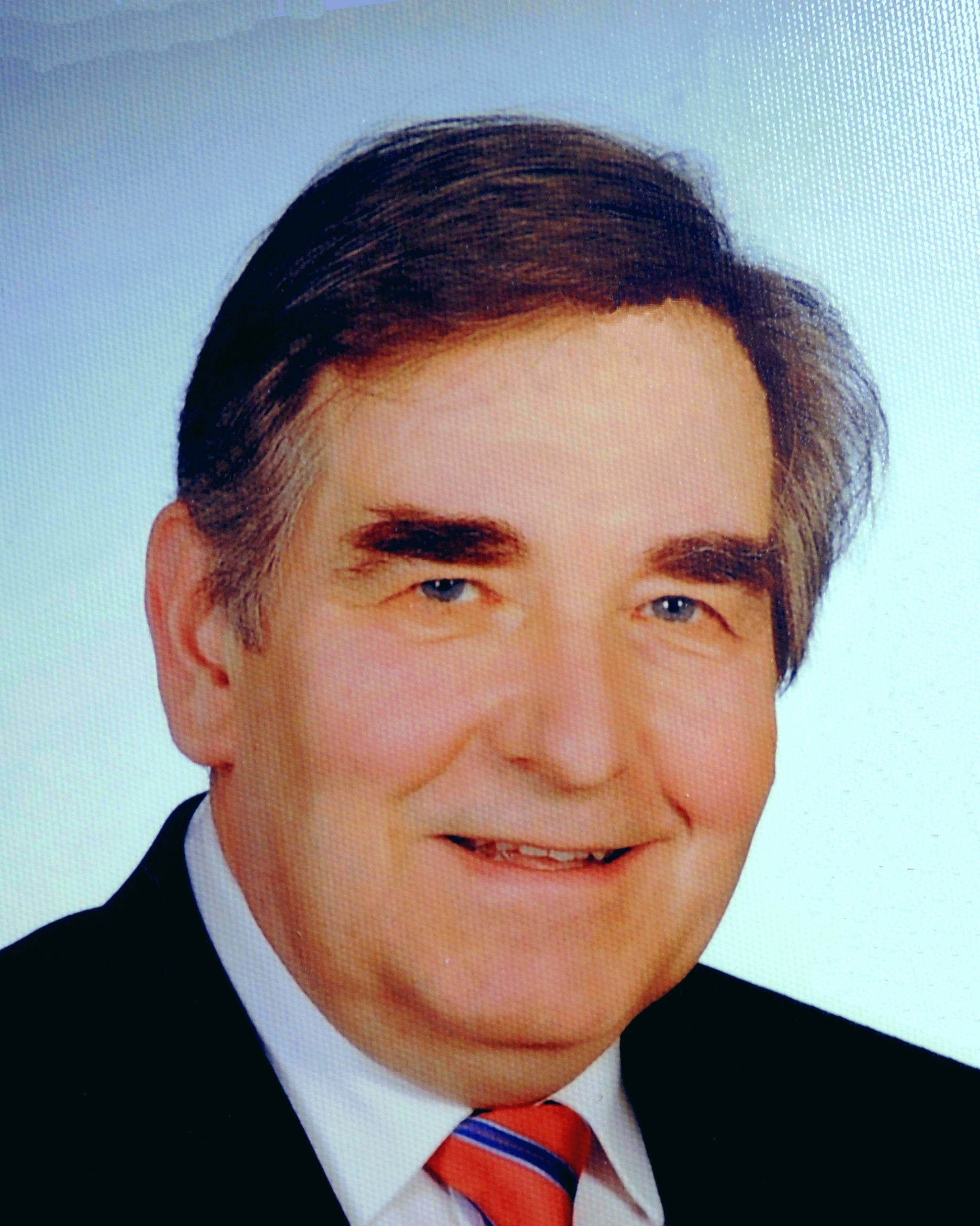
What are your hobbies?
(mountain) hiking, gardening, photography (and photomontages) and – how could it be otherwise – repair of equipment, machines, and devices with failures due to tribological malfunctions
Where do you work and what’s your position?
I retired from the TU Wien by end of 2014 but have still the possibility to work as a Principal Scientist resp. Key Researcher with the Austrian Competence Centre for Tribology (AC2T research GmbH) of which I am shareholder. After serving as a member of the management of this institution from 2002 till 2020, I currently still support the management as an authorised signatory.
How did you end up in the field of tribology?
As so often in life, chance or serendipity plays a certain role. As a young research assistant at the Vienna University of Technology in the early 1970s, I belonged to a group which, under the leadership of a dedicated lecturer, “discovered” the still young field of “tribology” for this university or for Austria. When the leader of this group was appointed as a professor, the question of succession in the leadership of the “tribology group” arose. A colleague of mine who was intended for this task at the time went abroad for some time at short notice for personal reasons in order to take on a completely different professional challenge. The “duty” then fell to me, although my desired scientific specialisation was medical technology. So I inherited first as a university teacher the field of tribology, which has stayed with me in several positions meanwhile for almost 50 years, there of the last 20 years demanding my particular responsibility for the founding, development and expansion of the Austrian Center of Competence for Tribology (AC2T research GmbH, Wiener Neustadt, Lower Austria).
Subsequently, other tasks were added, such as managing a consulting company in the field of tribology for several years in the 1980s and the responsibility as chairman (from 1986-2020) of the Austrian Tribological Society, founded in 1976 – both an excellent “training” for the preparation, foundation and long-term scientific management of the Austrian Competence Centre for Tribology (AC2T research GmbH).
If you were to explain “A” in the “Sendung mit der Maus”, how would you do that? If helpful, please feel free to add a schematic.
(“A” = squeaking/moaning/stick-slip …) “Sendung mit der Maus” could/can complement explanations by experiments or movies and similar augmentations of perception. This is not possible here, but some illustrations should help to create understanding.
Who of you doesn’t know this: squealing tyres, rattling brakes, screeching wheels of railway or tram cars? Some of you research pioneers have already cost your mother at home or your class teacher their last nerves because a window pane was made to sing, or rather squeak, with a wet finger or a moistened piece of polystyrene foam. (We don’t want to discuss the sanctions for this, such as a mobile phone ban!)
But who knows or thinks that all these unpleasant acoustic effects ultimately have one and the same cause. You may recognise the following common feature: in all these examples, (at least) two components are involved, i.e. tires on a track, brake pads with brake discs, railway wheels on rails and the wet polystyrene pad on the glass pane. But there is something else as well, namely that the components involved in each case move relative to each other – and in the cases mentioned, mostly at fairly low speeds, such as just before a vehicle stops until it comes to a standstill. The components described also act on each other with a certain force. Of course, otherwise a vehicle could not be braked. A railway train, for example, presses on the rails with its weight and, when cornering, on the rail flanks due to centrifugal force. For the polystyrene squeal, you also have to press on the glass pane (of course, only such strong so that it doesn’t break).
This is part of the prerequisite for the well-known audible effects in different applications, as described above: Two (mechanical) components with mutual force and relative movement are called a “tribosystem”. As a matter of experience, we notice that this movement is not always easy to achieve. Sometimes it is even quite difficult. You have to overcome a resistance. This is called friction. In many cases you don’t want any friction, but sometimes this force is needed, even necessary (for survival). One thinks here especially of situations such as those that happen in winter driving conditions and the tyres of a car lose their grip on the road.
Friction between the components concerned depends on many factors which can only be partially influenced in a targeted manner and which can also change in the course of the operation of a tribological system – due to interactions in the system, among other reasons. Particularly important are the materials used for the components (composition, hardness, etc.) and the changes they undergo, especially at the “friction surfaces”, due to the influence of lubricants, the movement conditions (we call them kinematics) as well as the surface shape and roughness of the surfaces in mutual contact.
You have certainly already noticed that you have to use force when you want to move, e.g., a piece of furniture. However, nothing happens at first, but suddenly the armchair gives way! So something must have changed in the frictional resistance. In order to describe the frictional effects in different applications (or systems) in a comparable way, one began already about 500 years ago (Leonardo da Vinci) to relate the determined frictional force to the force acting between the components, i.e. often the weight force, e.g. the vehicle weight acting proportionally on a tyre. This ratio of the frictional force to the so-called normal force is called the coefficient of friction. It now turns out that this coefficient of friction in one and the same system is usually strongly dependent on, among other things, the speed with which the two components move against each other. The highest coefficient of friction is found – with rare exceptions – when the two components are stationary in relation to each other. This is usually called static friction or – because nothing is moving yet and the two components adhere to each other – stiction. So you notice the initially higher force to set the furniture in motion (see above). Once the object slides, it suddenly goes more or less clearly easier. The furniture now slides, which is why the – now smaller – resistance effective in this process is called sliding friction (ref. Fig. 1).

Fig. 1: When it is intended to move an object it is necessary to apply an external force F which is initially balanced by a static friction force (frictional holding force FH) still lower than the maximum possible friction force FH,krit (1, 2) The external force is increasing till the friction response reaches its maximum FH,krit (3). Now the static friction is no longer able to resist a higher external force, and the excess of external force sets the object in motion (according Newton’s law). Suddenly the friction decreases (sliding friction FR), thus the external force needed drops as well (4).
This lower frictional effect once the object is moving also explains that if you start to slide somewhere, e.g. in the terrain on rocks, on inclined planes, you have hardly any chance to stop the sliding.
It may now be that a component in the tribosystem has the possibility of elastic compliance – either due to the material or surface properties or also due to the design of adjacent components, e.g. suspension of brake pads (Fig. 2 a). Due to the force required to initiate the movement, energy can now be stored through possible deformations (Fig. 2 b). As soon as the maximum frictional force possible under the given conditions is reached, the frictional connection is released and the component in question starts to move (Fig. 2 c). The elastic deformations “relax”, and the surface areas or components concerned initially move in the direction opposite to the relative movement of the counter-component (Fig. 2 d). But this counter-movement is limited at some point and the masses involved swing back, i.e. this time in the direction of the relative movement of the counter-component (Fig. 2 e). This can mean that for both components in the respective contact area (this can also be microscopically small) the same absolute speed of movement – thus standstill in relative terms – occurs for a short time. In this case, static friction or stiction prevails for the respective parts of the friction surfaces (Fig. 2 f). We thus have the same situation as in the previously described initial situation. If a “driving force” continues to be available, then the game begins anew (Fig 2 g): Deformation – loosening of the adhesive contact – backward and forward oscillation (at least for one component) – renewed adhesion, etc., etc. – the typical case of adhesive sliding or stick-slip motion.
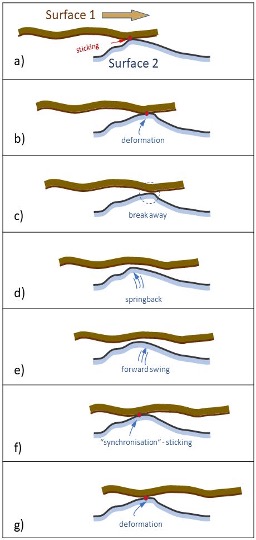
Masses and spring properties of the vibrating areas determine the vibration frequency and thus also the pitch of the acoustic effect triggered by the stick-slip motion. Small mass areas, such as in the vicinity of surface roughness, and little elastic deformation (high spring stiffness) mean high frequencies, as can be determined by appropriate measuring devices (microphones, usually structure-borne sound microphones attached directly to the object).
Such vibrations take place in the micro(meter) range and consequently in the not (any longer) audible range (this is then called ultrasound). However, such micro-vibrations can also excite larger structural components to (possibly audible) vibrations in their natural frequency. The larger the vibrating masses and the lower the deformation resistance (or the “softer” the deformable components involved), the lower the frequencies of these special cyclically occurring processes in a tribocontact. Thus, the range of pitches of these triboacoustic effects includes the low infrasound range up to high ultrasound, in each case also in the inaudible range. Low frequencies in the range audible to the human ear can be perceived as rumbling, humming or bouncing. The high frequencies correspond to typical chirping, whistling, squeaking and “singing” noises, even if this singing is mostly not a pleasant sound.
Singing noises, or better: sounds, are also produced by playing a violin – or any other “string instrument” (it can even sound pleasant if someone is a professionist to do it). Yes, that’s right: When moving the violin bow over an (elastic) tensioned string, the process takes place exactly as described above. Note: The low sounds are produced with comparatively thick – and with greater mass – strings. The tension and free vibrating length of a string – and thus its elasticity – determines the respective pitch or sound character. The cyclic process of stick-slipping is continuously triggered during the bow stroke. In comparison: When playing the guitar (as well a stringed instrument, but not a bowed instrument), on the other hand, the strings are plucked, so it is not really a jerk “slide”. In addition, the “adhesive contact” for a played note is only made once by the plectrum, the string then vibrates out without further stimulation with corresponding damping. Thus, friction plays almost none the role in comparison to plucking.
Now another example of stick-slip motion should be mentioned, which is located in the extremely low infrasound range. It can therefore not be perceived by the sense of hearing. However, the vibrations in question are perceived by our sense of equilibrium, possibly by the sense of touch and, in bad cases, also visually: These vibrations are caused by earthquakes. Huge masses are involved, the earth’s crust is under tension due to hardly noticeable displacements, often “built up” over many years, The displacements and tensions suddenly become free when the cohesion of the huge components is no longer sufficient (possibly also due to tidal effects, i.e. the gravitational influence of the moon and the sun on our earth). Then a “rumbling” occurs, whereby secondary effects also make a humming or similar audible. The vibrations of parts of the earth’s crust can lead to landslides, faults and cracks in the terrain, catastrophic destruction of buildings (roads, houses) and unfortunately also fatalities. The tectonic vibrations (i.e. those occurring in the earth’s crust) are often perceived by sensitive measuring instruments (seismographs) even over thousands of kilometers and recorded for evaluation.
From what has been told, it is clear that friction vibrations can be predominantly unpleasant or in some cases even highly dangerous. Thus, at this point at the latest, the question arises as to which conditions lead to stick-slip and how these can be influenced in order to avoid stick-slip. We have already heard something about the basic components and conditions of the “tribosystem”, especially about the deformation behavior. Regarding the influence of the coefficient of friction, we know that a significantly higher static friction (compared to the sliding friction once the component starts moving) basically favors stick-slip, if not even causes it (together with other parameters). Moreover, a higher (static) friction coefficient level enables to a greater extent introducing deformation energy into the system in question. In this case, vibrations with a relatively large amplitude occur when the elastic energy is “released”. Such vibrations can therefore be perceived more clearly acoustically or haptically (by touch). One can now cleverly apply this knowledge to deal with the problem of stick-slip. Accordingly, one acts on the problematic system under consideration, i.e. in the case of stick-slip, in order (1) to at least lower the friction coefficient level, (2) to (strongly) reduce the drop from static friction to sliding friction or (3) to achieve a larger (!) sliding friction coefficient in relation to the static friction coefficient – theoretically absolutely effective, but only difficult or rare to realize.
Apart from measures to reduce the elasticities in the frictional contact or the adjacent mechanical structures, this primarily calls for the use of lubricants if possible. Reasonably, their main task is to reduce (or control) friction. Furthermore, also special additives can suppress or prevent stick-slip, for example in roller bearings or gear drives. However, classic lubricants (such as oils or greases) cannot be used everywhere. In this case, one can try to help by using materials known to be favorable from a friction point of view for at least one of the components of the tribological system (also combinations, especially certain polymers) or also special surface coatings. Good experience has been made with the use of fluoropolymers (most commonly known as “Teflon ®”), e.g. as a powder additive to greases, pastes and bonded coatings. For the system wagon wheel/railhead flank, spray water is occasionally used as a lubricant – any time before a train passes – inexpensive, environmentally friendly and quite effective.
Now, there is no “panacea” in tribology either, or there can also be “side effects”! It can happen that lubricants change their properties when used at low temperatures – they become “thicker”, more viscous – which leads to stick-slipping under such operating conditions despite lubrication. The “cold squeal” – if in the audible frequency range – can be extremely unpleasant and therefore impair the quality of a product.
Combating earthquakes with the knowledge of stick-slip also has little chance. How could one find and use suitable (environmentally compatible!) lubricants? Not to mention the fact that nothing can be done about the “materials” of the components involved (in this case minerals, which are often not even known in detail). Moreover, accessibility to the friction partners of seismic activity is often not given. The introduction of press water, quasi as an eco-friendly lubricant, is probably (at least according to current possibilities) more in the realm of utopia. However, it seems realistic to use tribotechnical knowledge gained from rather “everyday” systems from modelling and data evaluation with the help of artificial intelligence methods also in the context of earthquake research or earthquake warning.
Now it would be interesting if you could find other objects or “structures” apart from the examples mentioned at the beginning, where friction is often a decisive – positive or negative – effect or where frictional vibrations may also occur. So we need two components in contact under the effect of force and relative movement.
How far does your imagination go? Look for examples in everyday life, in devices, machines, in production processes, in crafting, sportive activities, in the interior of the human body, a.s.o., a.s.o.
What is your personal perception of stick-slipping in everyday life? How would you classify, e.g., the chirping of a cricket – a stick-slip process or rather a fast stringing? (https://youtu.be/CPCfUQ_iQps)
You can also play a competition: Who knows the most examples in a given time? Who found an example the fastest? Of course, examples that are already known do not count!
Do you have any favorite anecdote about the broad field of tribology?
Why not even three of them (and not necessarily with the specific thematic focus):
It was the 1980s: A tribology conference (with sparse international participation) in the former Soviet Union came to an end. The functionaries gave their programmatic closing speeches. Among other things, they asked the participants to express their comments (criticism), and so the “Closing Session” dragged on. One American tribologist – very pragmatic – slowly but surely lost patience and said: “Why are they doing this? When it’s over, it’s over!”
A German tribologist who is well known far beyond the borders of his home country found that his “favourite specialisation”, lubricants and lubrication technology, was not sufficiently represented in a well renowned tribology conference. He expressed his relative disappointment to colleagues, saying: “There’s too much tribology here and not enough lubrication engineering!”
On the occasion of the 50th anniversary of the official presentation of the term “tribology” (actually presentation of the so-called “Jost Report to the British Parliament), about 150 tribologists from all over the world were received by His Royal Highness Prince Philip at Buckingham Palace, London, in March 2016 on the initiative of the father of tribology H. Peter Jost. The crème de la crème of tribology chatted animatedly in the Royal Gallery and awaited the arrival of the host. Amidst the general murmuring, it was completely lost that His Royal Highness – accompanied by his personal adjutant and the ITC President Peter Jost (incidentally of about the same age and similar sprightliness as His Royal Highness) – entered the hall. Prince Philip tried to begin his greeting address, but the noise level hardly diminished, let alone anyone taking notice of His Royal Highness. Peter Jost banged his fist on the prepared lectern (presumably from the Empire style period, given the dignity of the location and of the occasion) to make himself and his host heard, which finally succeeded. Peter Jost’s “attack” on the good furniture was commented by His Royal Highness – now clearly audible – with a dry British “Oh, my furniture!
If you had one wish with the “Young Tribologists”, what would you wish for?
Expand and strengthen communication among each other, advocate that tribology and tribology-related topics be included in the various levels of technical/scientific/technical education, be open to the integration of tribological knowledge into other disciplines and vice versa. (Sorry, these are more than one wish!)
Which trends would you see in the field of tribology, especially which applications do you think would gain increasing importance in the future?
Unavoidably: Reliability and service life extension of production facilities, (further) energy minimisation and smart maintenance in the transport sector, in processing technology, and in the primary industry.
What do you think are the three most relevant competences for somebody working in the field of tribology?
Creativity (ability to see or make cross-connections), perseverance, and the ability to work in a team
Optional: Any other question?
Just to initiate a transdisciplinary reflection:
Is tribotechnical knowledge in a figurative sense somehow useful to make our social interactions on different levels better, more pleasant, more successful, i.e. to avoid friction and wear and tear in this area as much as possible?
I am convinced that it works!